#1 DESIGN PROPOSAL
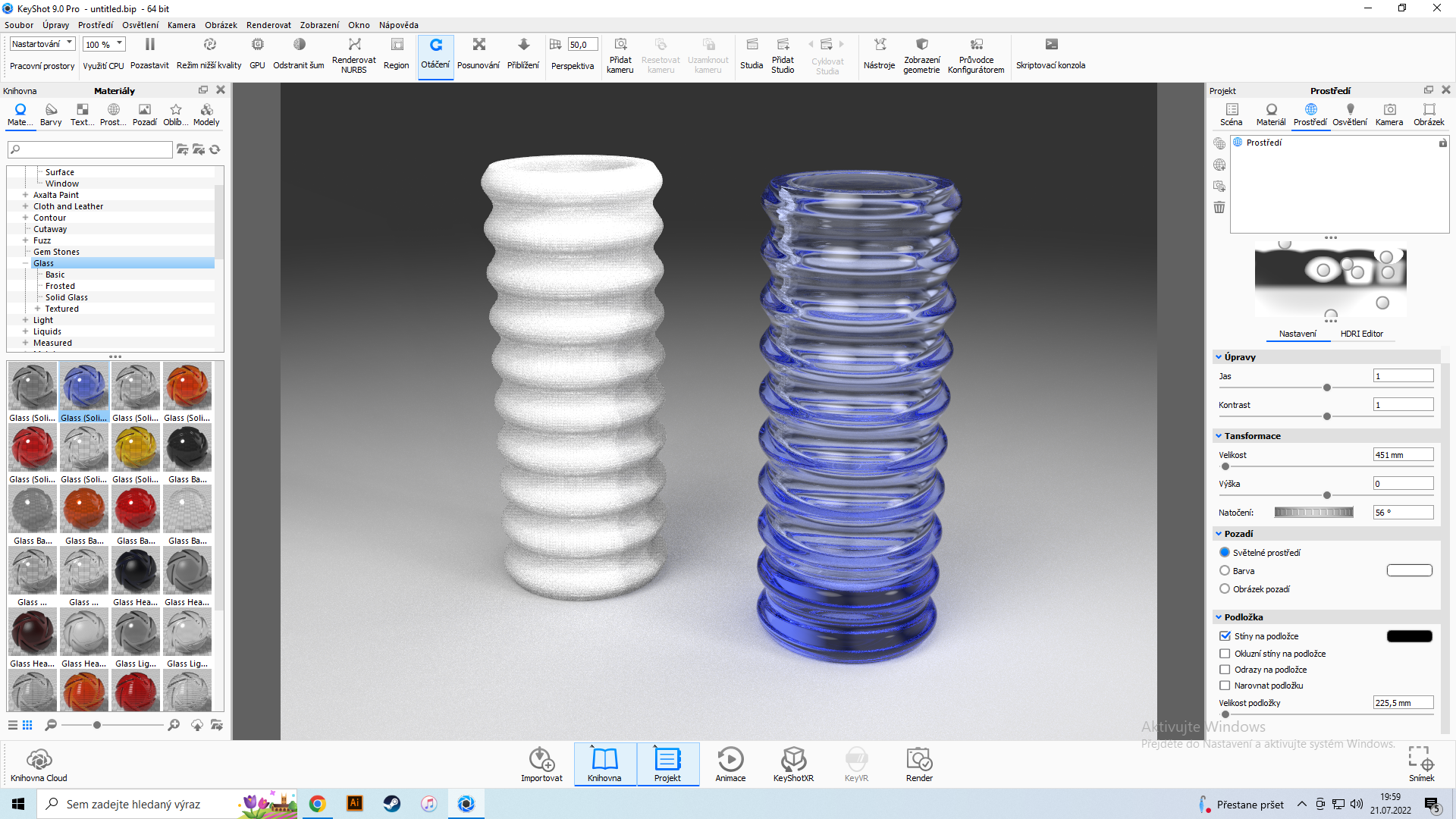
It all starts with an idea, a technical drawing and a 3D design of the product. After a suitable shape is created, a drawing is printed or drawn to produce the glass mould.
#2 MOULD PRODUCTION
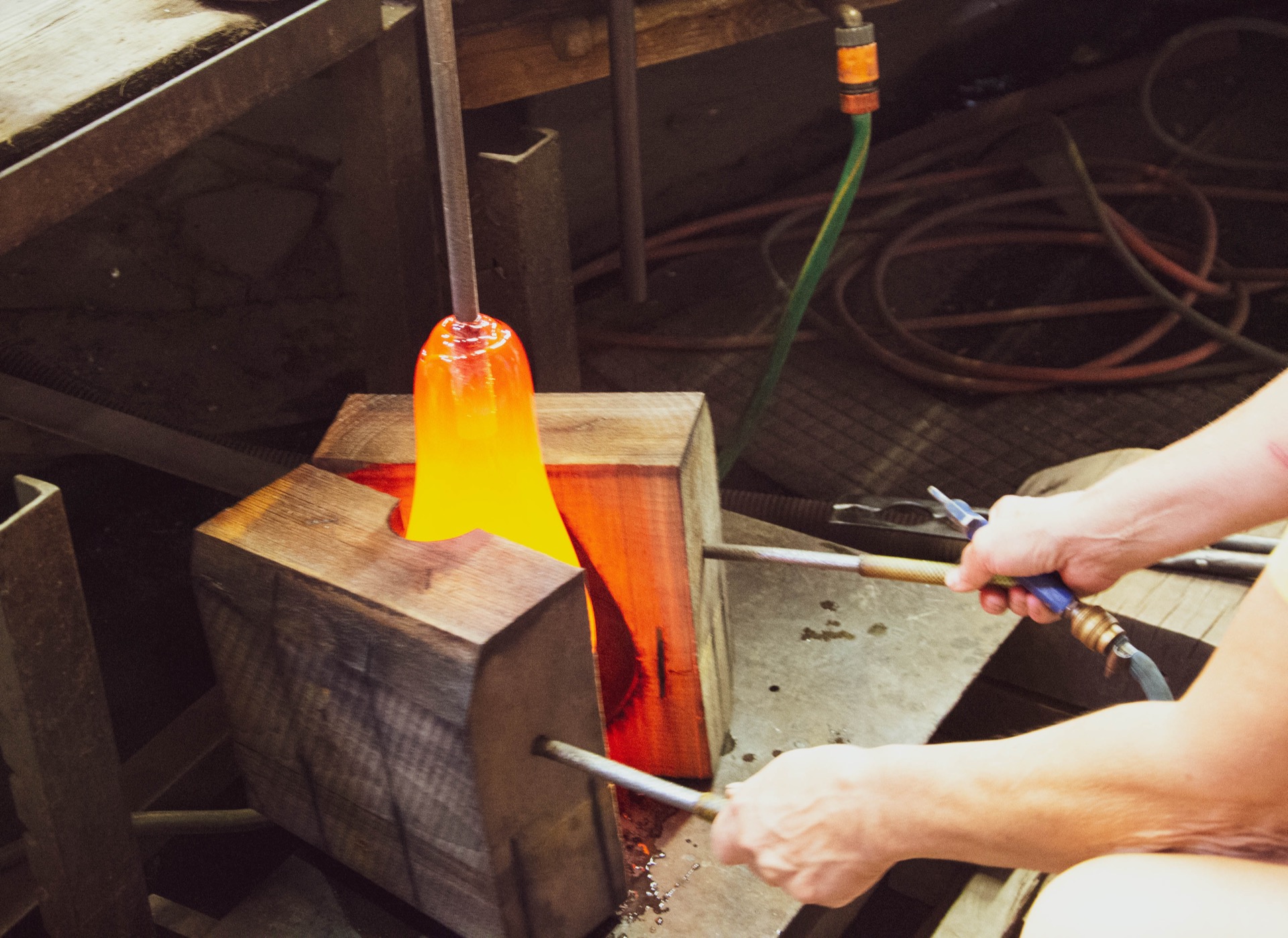
The proposed drawing is handed over to the moulder, who then creates a wooden mould according to the design.
#3 GLASS BLOWING
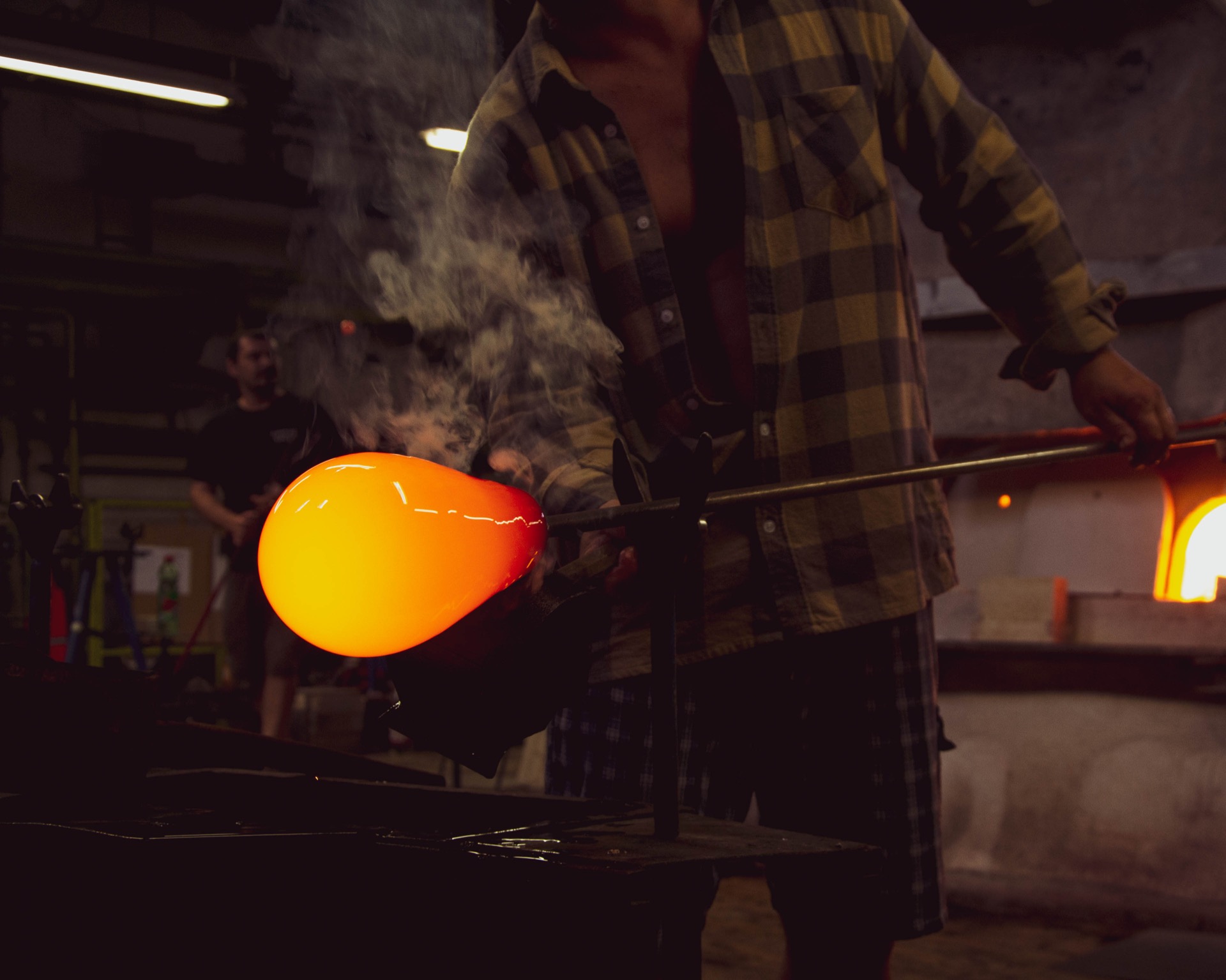
The produced mould goes into the hands of the glassmaker, who creates the desired shape using a blowpipe. Next, the glass is moved into a cooling furnace. The cooling process takes several hours or days, depending on the thickness of the glass. If the glass is not cooled carefully, it can lead to cracking due to internal stress.
#4 GLASS CUTTING
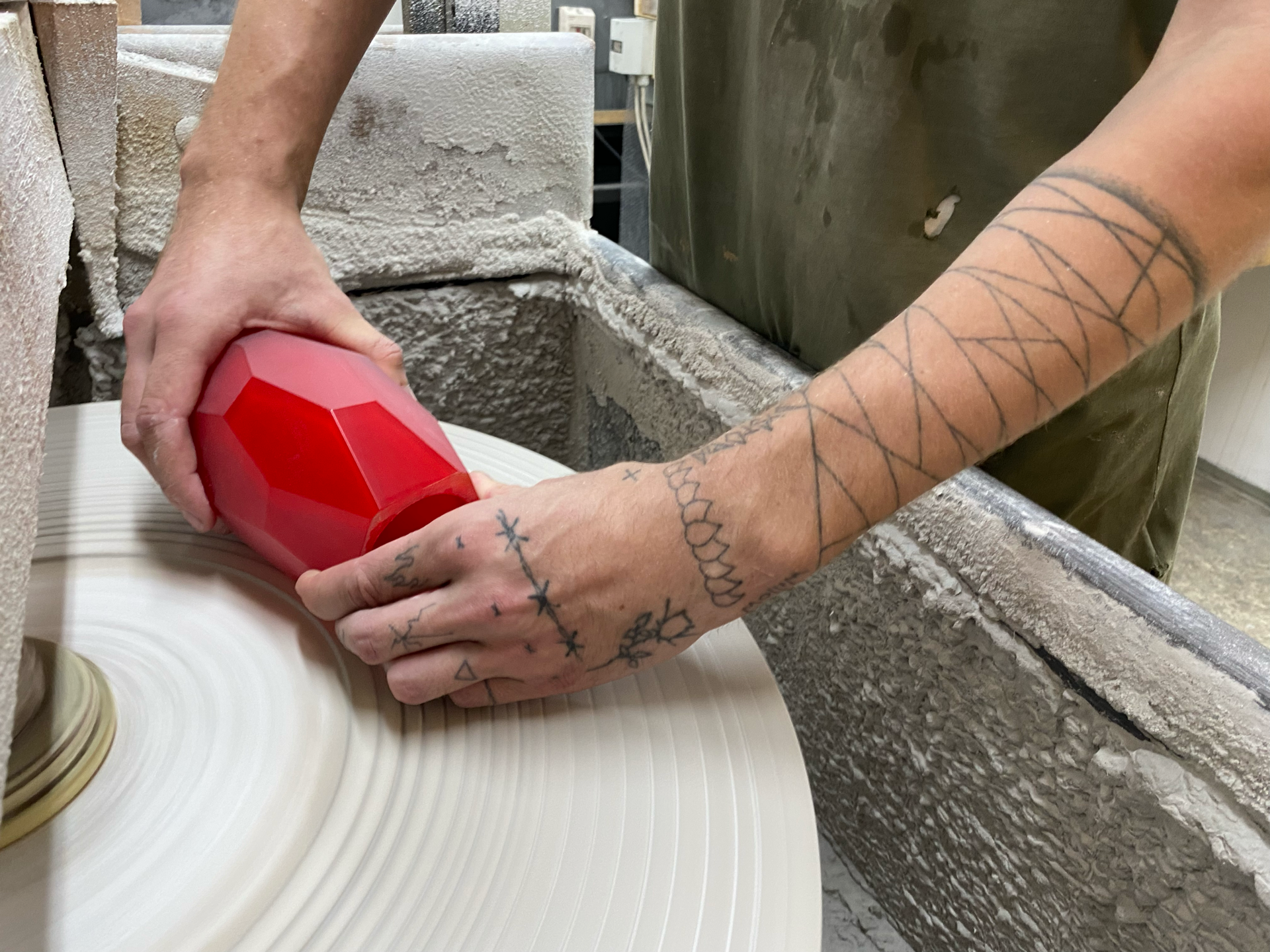
Each blown glass piece passes through the hands of skilled grinders who, over several hours of meticulous work, shape and polish it to perfection. The process involves four grinding wheels – starting from the coarsest to the finest. It begins with rough shaping of the edges, followed by progressively finer grinding and polishing. Thanks to this careful step-by-step craftsmanship, the product achieves its flawless form and distinctive shine.
#5 SANDBLASTING AND LACQUERING
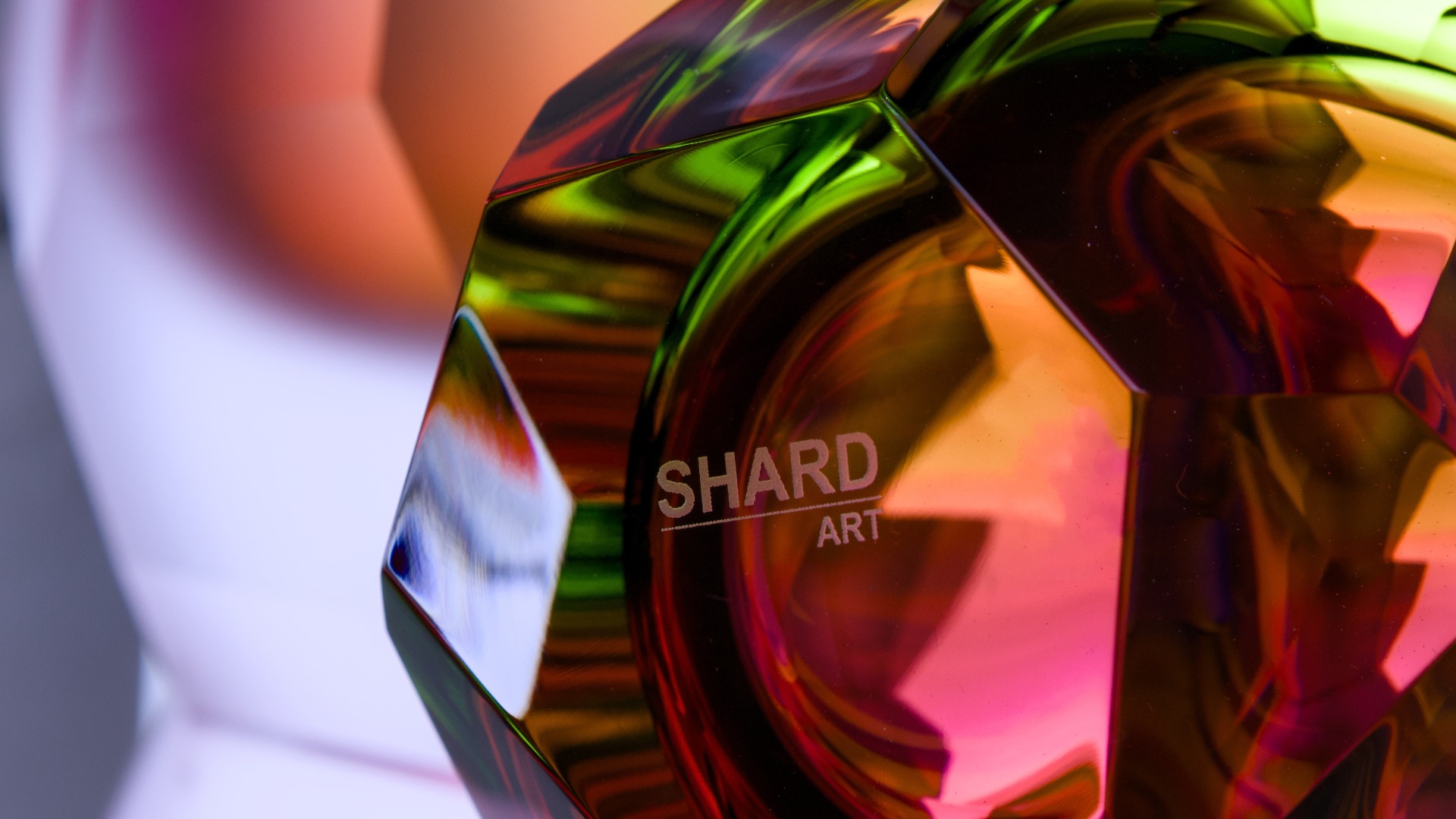
In the case of some objects, it is necessary to use sandblasting or lacquering. Sandblasting is used for virtually every product to sign the logo on the bottom or to frost larger areas. Lacquering is used only occasionally to finish rough or sandblasted glass surface in order to protect it against fingerprints, grease, or just for a glossy effect.
#6 FINAL PRODUCT
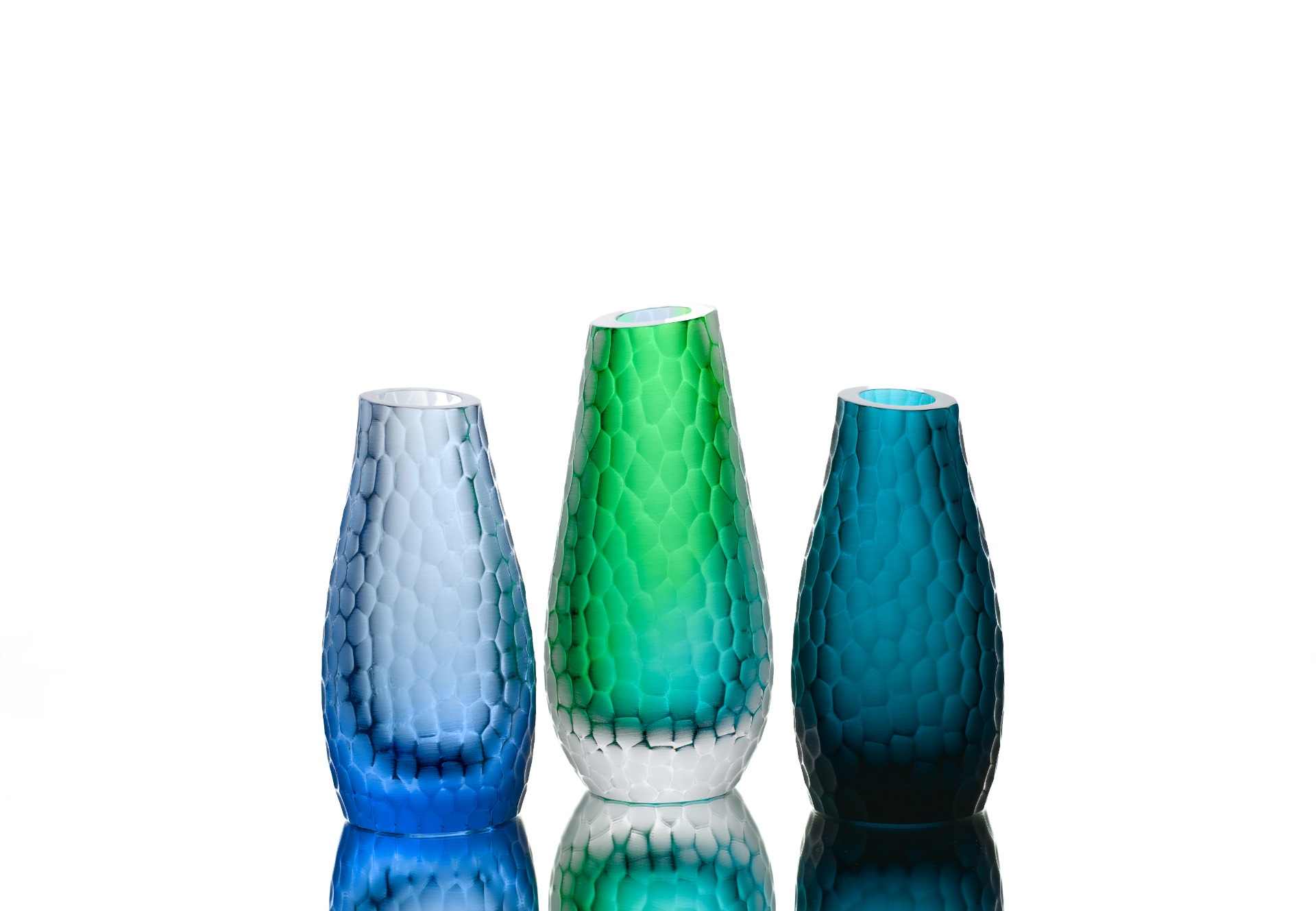
The final product is packed in a padded box and ready to be sent to your hands.